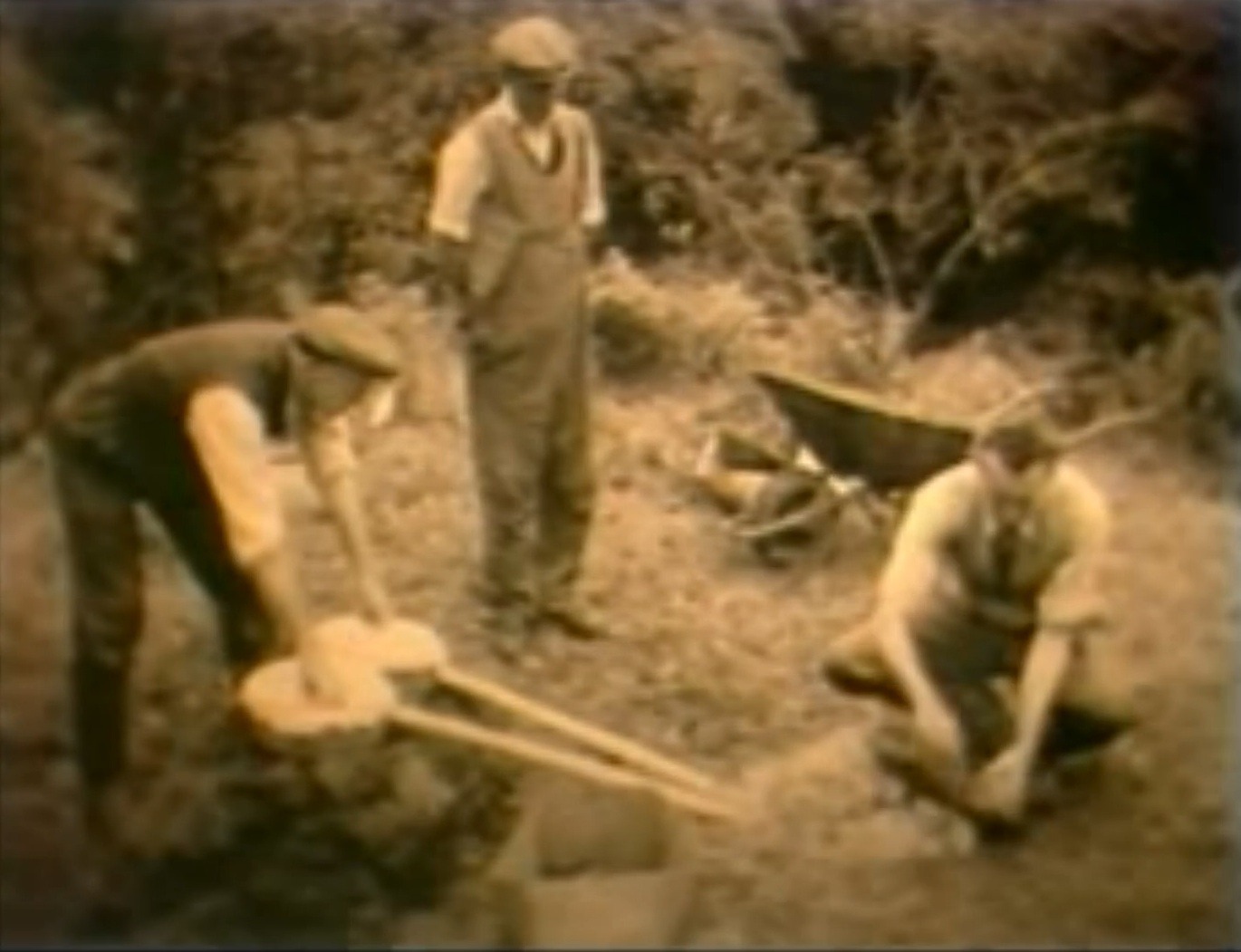
In late October, 2024 Irish archeologist Brian G. Scott flew to my humble home here in Vermont and we commenced four days of iron smelting. This focus of our endeavor was reconstructing and testing the viability of a furnace constructed and documented by Michael O’Kelly in Ireland in the 1950’s. Although there is a small amount of film footage of his experiments, the documentation of his methods were otherwise quite poor, and to add to that his resulting blooms have been lost from the museums that once kept them.
The bowl furnace has been a contentious debate in the archeological community since before O’Kelly performed his experiments. Though there is evidence for their use in various parts of the world, such as Africa (“Traditional Metalworking in Kenya” Jean Brown), some think the bowl furnace makes no sense both practically and when put into the historical context of copper smelting and the evolution of the shaft furnace. Some questions that arise are: why would people utilize such a “primitive” furnace design in the early iron age if taller, more effective, shaft furnace technology was already understood by the end of the bronze age? If the bowl furnace was utilized by peoples of the past why has the experimental archeology only provided examples of poor efficiency in terms of iron yield and quality? Why is there a lack of archeological evidence for these furnaces?
On the other side, some believe the bowl furnace was not only viable, but likely utilized through out history including Ireland; Brian Scott being one of these people. Was the bowl furnace indeed viable given a nomadic setting or a minimum of resources? Could the archeological finds often thought to be the base of taller shaft furnaces actually be the remnants of a bowl furnace? There are many questions surrounding the bowl furnace and our experiments only touched a few of these. Over the four days we, along with the help of iron-smelting friend Nick Tomlin, we conducted three smelts in the domed bowl-furnace (there doesn’t seem to be a consensus in the archeological community on the definition of the various morphologies of bowl furnaces. For that reason I will simply call what we made a “bowl furnace” for simplicity).

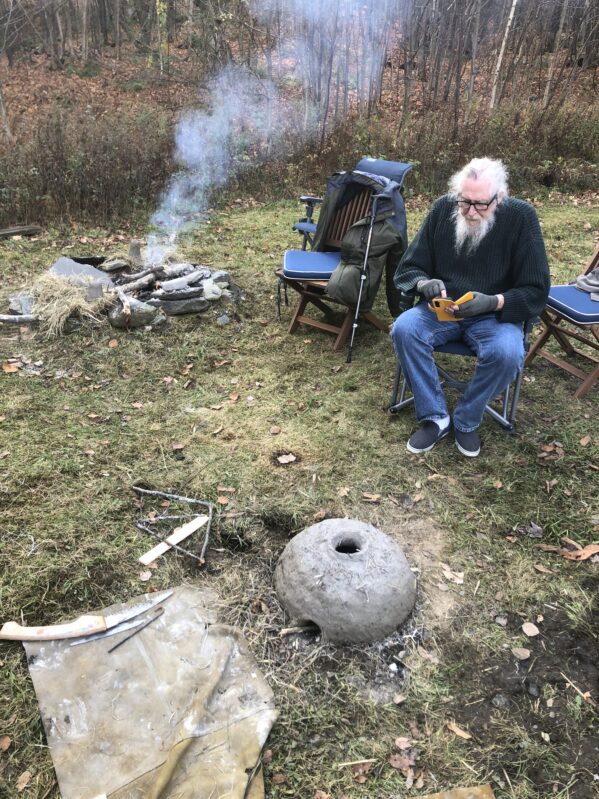
Our furnace design deviated from O’Kelly’s in that we created a removable dome over the bowl. O’Kelly had to destroy the dome after each of his experiments in order to access the bloom. Three smelts were completed over the four days. The first was a direct replication of one of O’Kelly’s experiments in which the powdered ore was placed into the furnace before the smelt began and was allowed to “bake” in the hot reducing carbon monoxide gas over the duration of the smelt. Our clay tuyeres (air pipes) were based on archeological finds in Ireland.
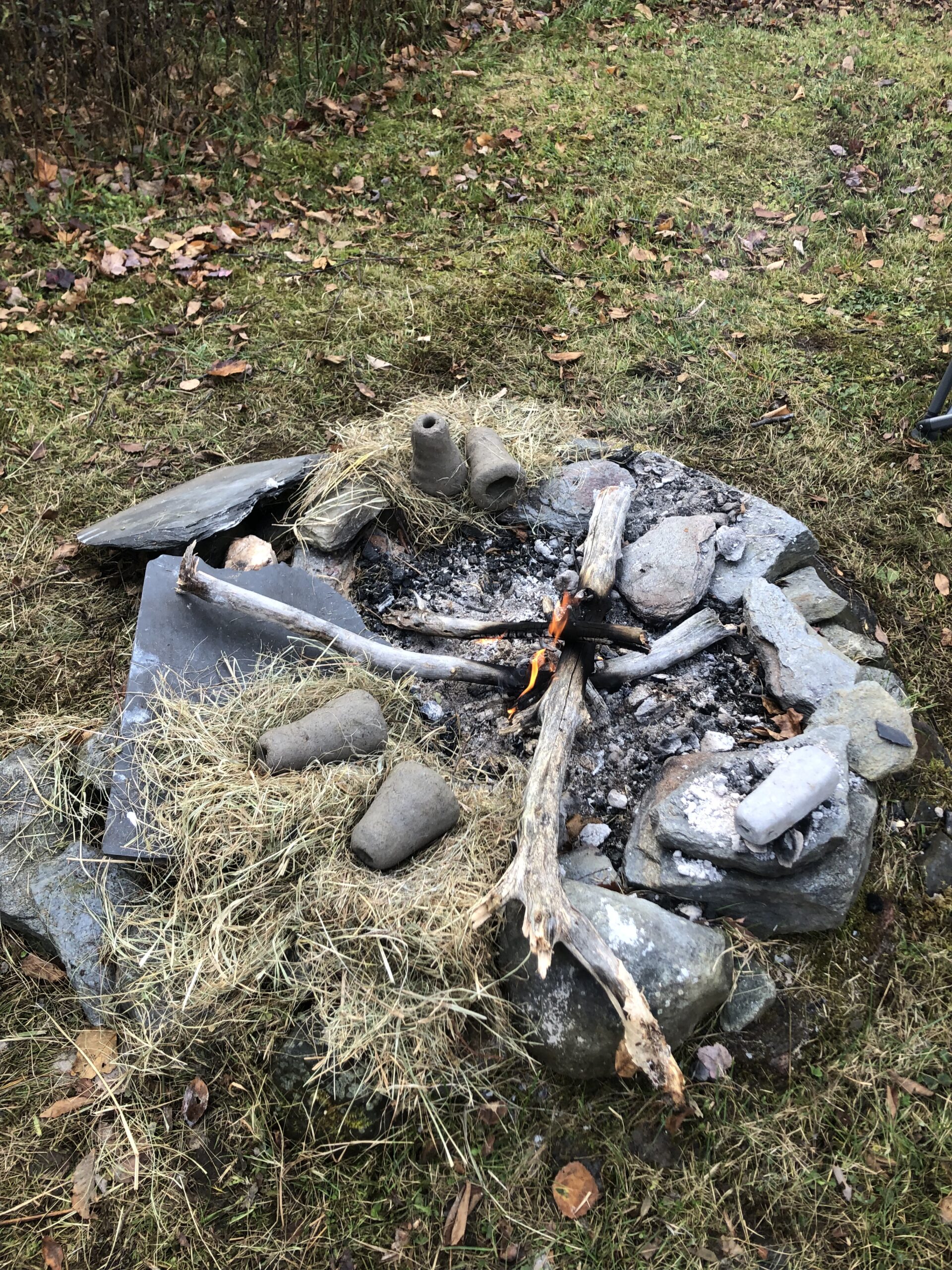
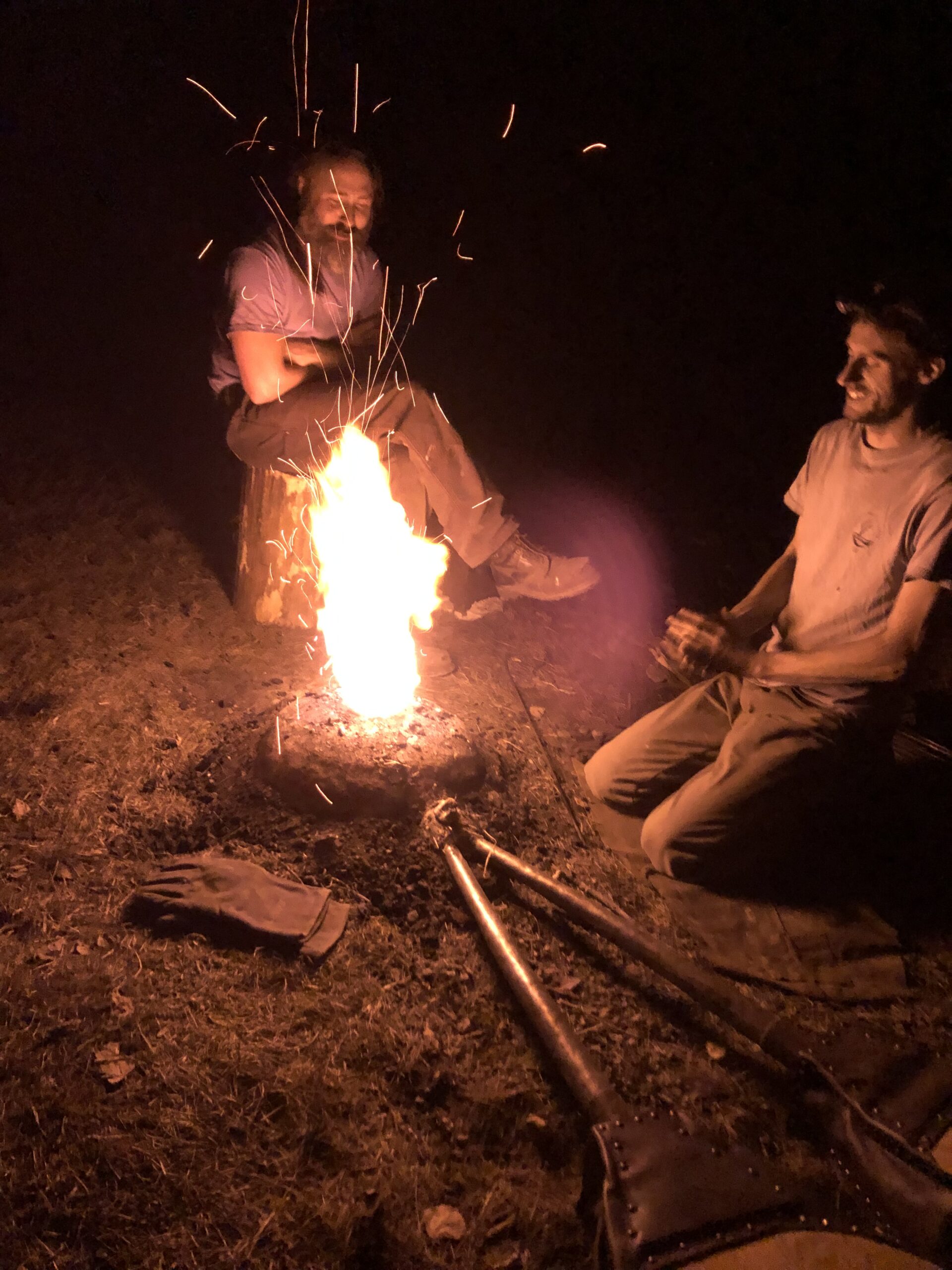
Our second and third experiments were run more like we would a shaft furnace: feeding ore into the top through-out the duration of the smelt. Our result in the second smelt was a small piece of forgable iron mixed with a lot of slag, which made for difficult forging. That said, it proved that our method and the furnace design was capable of reducing iron oxide to a pure, ferrous, form. For our third smelt we made some adjustments- powdering some of the ore as fine as we could and changing the angle and penetration distance of the turyere. We succeeded in smelting a small dense piece of forgable iron (right piece in right photo below) as well as a bunch of smaller bits and gromps (partially reduced bits that fall off from around the bloom). When we saw that we had a lot of small pieces of iron smelted, we made the decision to quickly shovel out our smelting furnace, change the floor depth, and run it as we would an Evenstad style remelting hearth. We added all of our pieces back into the furnace, consolidating and cleaning the metal of slag. We pulled out this new, remelted, bloom and our result was a much larger and workable piece of iron. We changed our bellowing speed and turned our now remelting hearth into a forge, working the new piece of iron down to a sharp point, proving that it was indeed a usable and quality piece of iron. Using the bowl furnace in this way: smelting with it, converting it to a remelting hearth, and finally using it as forge- was a significant increase to the efficiency and productivity of this process. It is normal for archeologists to find an ironworking site and designate it as either a forge, smelting furnace, or other based on the slag and other remnants. This idea that perhaps people of the past could have used a single clay structure for multiple processes could help illuminate some of the confusing finds at these ancient ironworking sites, and perhaps give credibility back to the bowl furnace as a feasible technology given the proper circumstances.
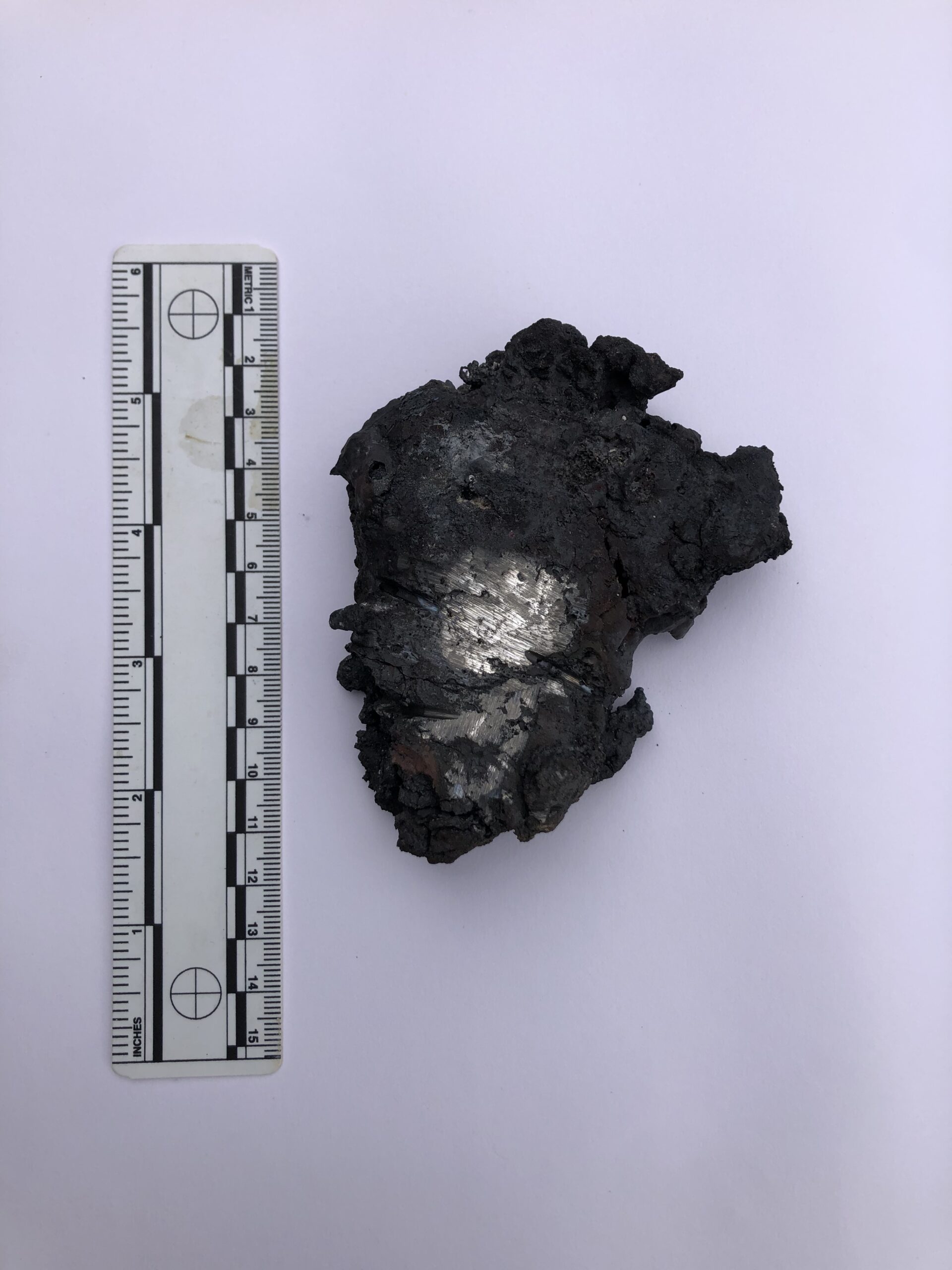

The iron was then forged into a replica hand sickle based on an archeological find. The goal here is multi faceted. This gave me a chance to judge the quality of the metal through the forging process. I had to fold the billet a few times, but it quickly worked up into a nice bar that i was able to draw out into the sickle shape. This forging process allowed me to judge the iron quality, the slag quality, if there are any elements in the iron that might alter its characteristics (phosphorus or sulfur, for example). The sickle was then cut into pieces and dropped in the mail to Ireland, where Brian will be analyzing it with a microscope using metallographic techniques to compare our material to historical ones and illuminate more about the micro structure of the metal.
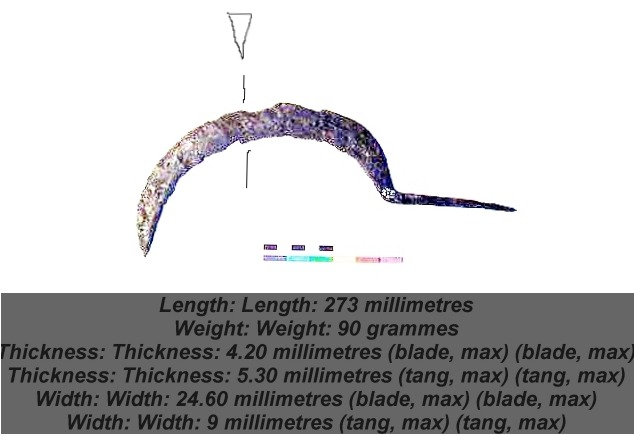
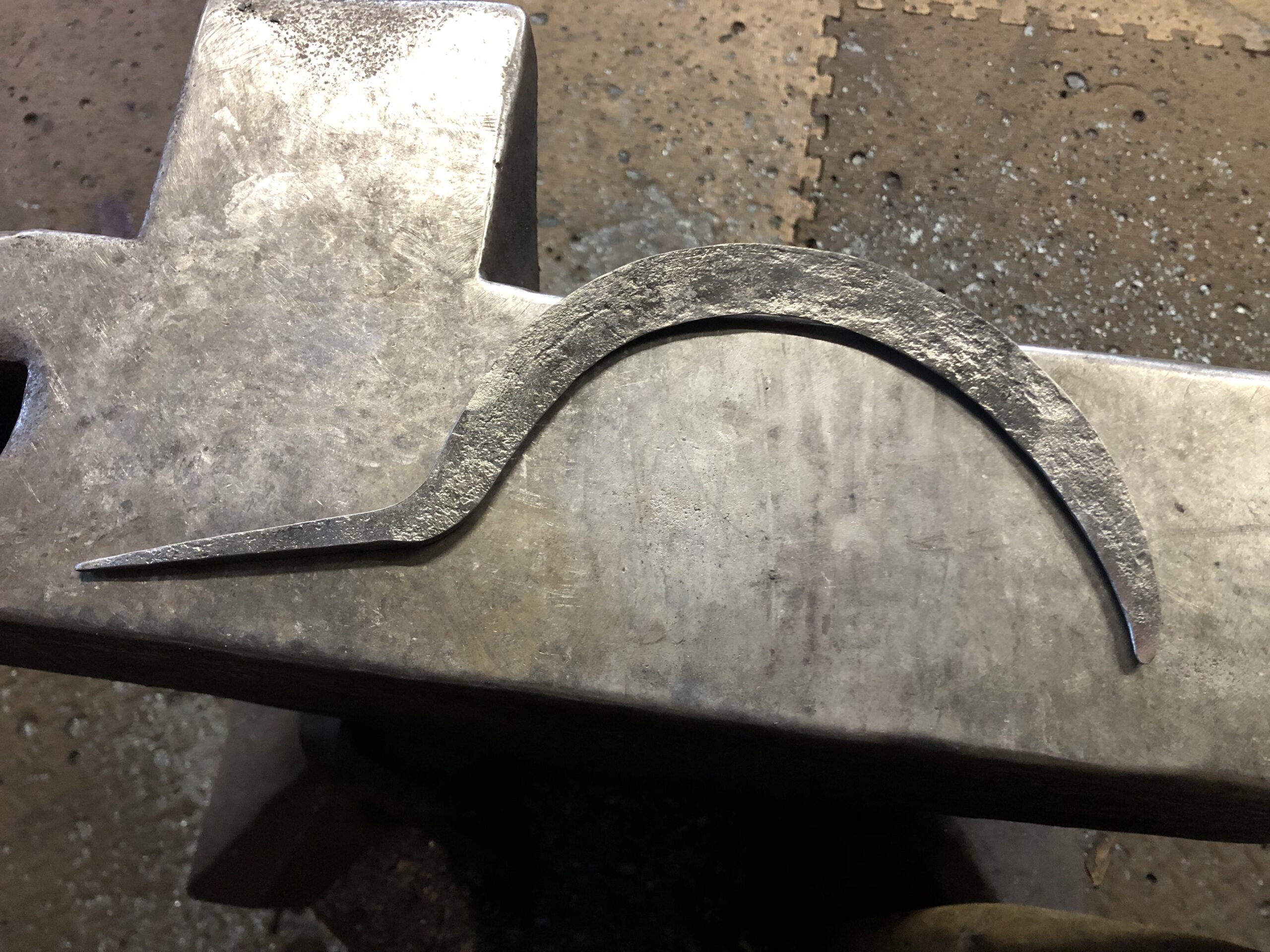
The furnace did not survive the harsh, Vermont, winter. This gave us an opportunity to analyze how a bowl furnace such as this degrades through out the course of year. A new furnace was rebuilt, and soon our next round of experiments will begin. Can we replicate the process of smelt 3 while improving efficiency and productivity? Can we remove the dome and still achieve similar results? Can we replicate the results with a different ore source, perhaps a fine magnetite powder? Many questions to answer still.
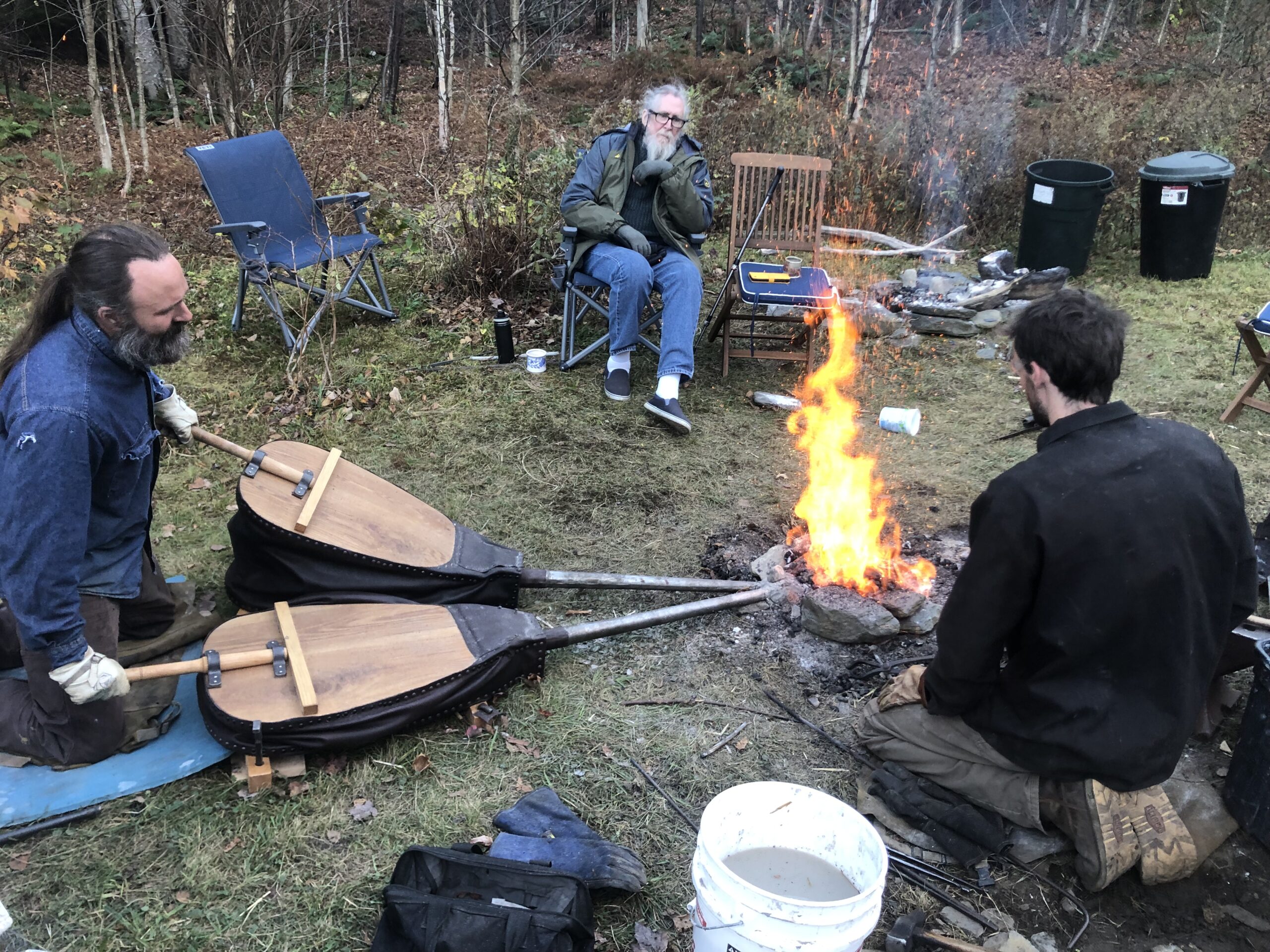
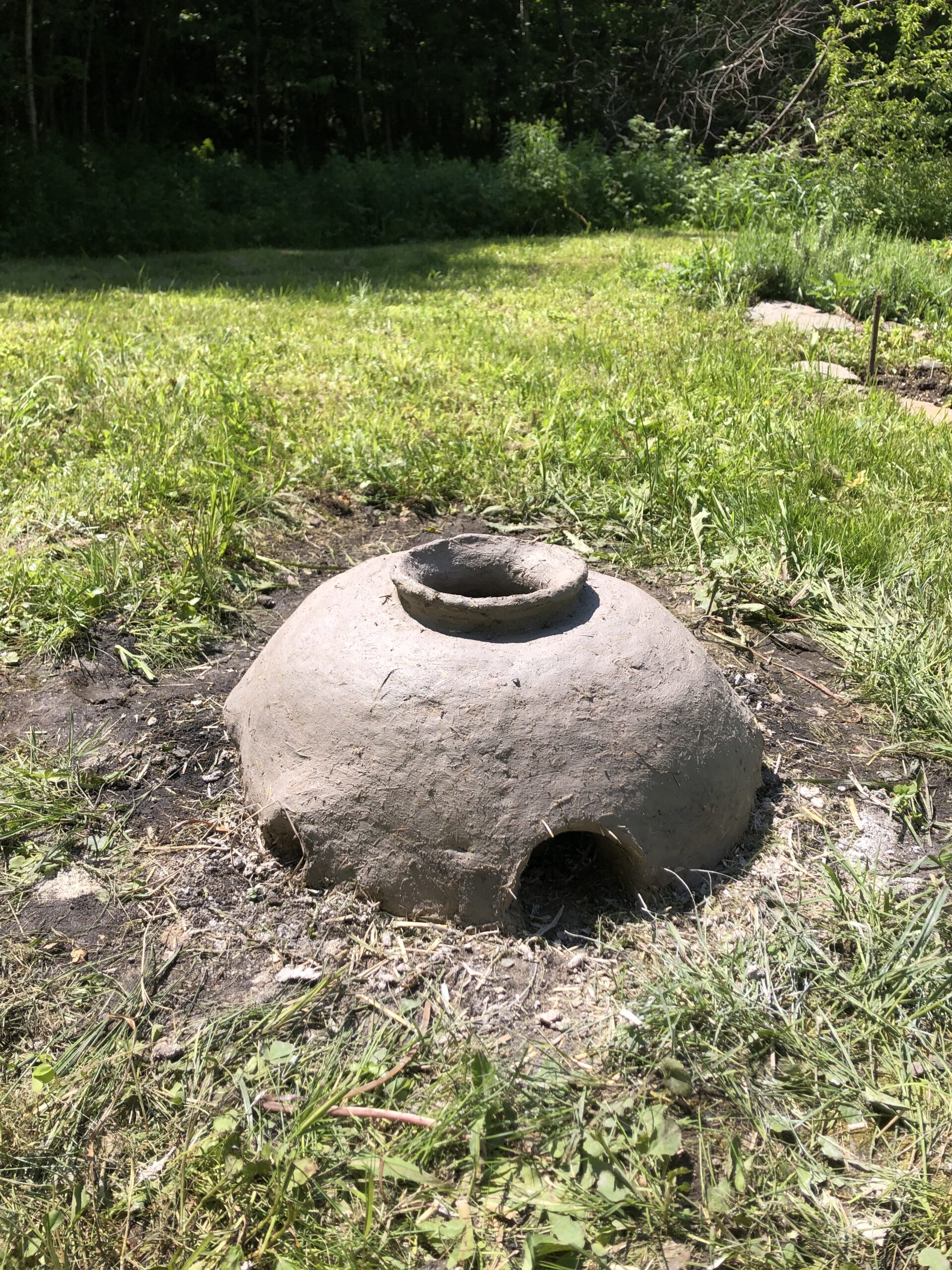